Precision without Poisoning: Plasma Emission Monitoring in Reactive Sputtering with KDF Technologies
In the high-stakes world of thin film deposition, especially for functional oxides, nitrides and other compounds made by reactive sputtering with metals, precision is everything.
For example, slight variations in nitrogen content can impact the color of titanium nitride films dramatically. Figure 1 shows a variation in color, based on nitrogen content, for titanium nitride thin films deposited by reactive sputtering. Reactive sputtering, when done precisely, walks the fine line between optimal compound formation and catastrophic instability caused by target poisoning.
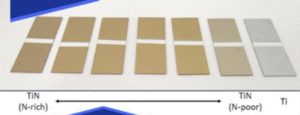
For scientists and process engineers new to the field of thin film deposition, one critical lesson must be learned: the difference between success and failure in reactive sputtering lies in millisecond-level process control. This is where Plasma Emission Monitoring excels as a process control tool and why KDF Technologies has emerged as a leader in enabling production-grade precision on its in-line batch thin film sputtering systems.
The Reactive Sputtering Challenge
Reactive sputtering involves doing some inorganic chemistry in the sputter plasma, or at the surface of the substrate. That is a discussion for another article. Typically, a metal target is sputtered and the resulting sputtered adatoms collide and react with active gases, such as oxygen or nitrogen, introduced into the system, forming the desired product, such as SiO2 or TiN, as a thin film. Unfortunately, during the reactive sputtering process, if not controlled properly, some of the reacted material re-deposits on the surface of the target, masking some portion of the metallic sputter track, preventing it from being sputtered as a metal. If a sufficient amount of reacted material blankets the surface of the target, it becomes ‘poisoned’, where an insulating, non-metallic, layer builds up on the target surface causing the sputter rate to crash. Figure 2 shows the impact of nitrogen reactive gas flow on deposition rate, as the target gets poisoned.
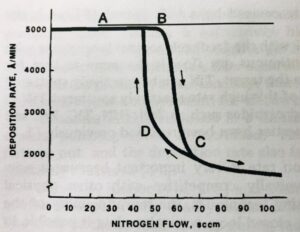
The goal? Stay in the sweet spot of the deposition process where sufficient reactive gas is supplied to make the desired film, without an excess of reactive gas causing re-deposition and poisoning at the target surface. Achieving this balance requires real-time feedback and sub-second responsiveness, which traditional gas delivery systems, like mass flow controllers, with their 250 millisecond response times, struggle to deliver.
Enter Plasa Emission Monitoring: 100 Millisecond Insight
KDF Technologies’ Plasma Emission Monitoring System (PEM) provides a solution to precision control of reactive thin film deposition processes with near 100 millisecond response times to changes in plasma conditions that promote poisoning. This is more than twice as fast as conventional mass flow controllers which work off of total system pressure, for instance. The monitoring of optical emission spectra of ionized species, rather than total system pressure, provides near instantaneous insight into the chemical composition of the plasma and serves as a window into the composition of the thin film as it is deposited. If the reactive gas species, for example nitrogen or oxygen, begins pushing the limits of the process and threaten to move the gas mixture out of the ‘sweet spot’ toward poisoning, the PEM system will detect an unfavorable mixture of precursors and automatically, within 100 ms, adjust the reactive gas flow- in real time.
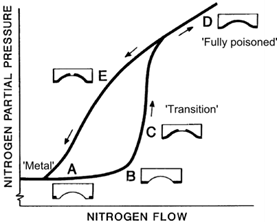
This is more than monitoring the condition of the plasma, it is about control. The PEM systems provides a closed-loop feedback mechanism, which dynamically stabilizes the deposition process while maintaining conditions which optimize sputtering and deposition rates as well as film stoichiometry.
Batch Production with Precision: The KDF Advantage
KDF’s in-line sputter systems benefit from 50 years of experience providing batch thin film production for industries including medical, electronics, solar panels, and sensors. The systems are particularly suited for batch production of high-performance nitrides and oxides through a combination of mature, robust, system design and PEM controls.
Key System Features Include:
- Optimized Gas Rings: These gas-channeling structures send reactive gases directly into the sputter plasma at the target surface where they will be most effective, in terms of reactivity and stoichiometry control, particularly with challenging gases like diatomic nitrogen.
- Fast-Response Mass Flow Controller Placement: KDF systems are designed so that there is minimal latency between a control signal and the flow control function, by positioning the mass flow controllers adjacent to gas injection sites, minimizing delays, enabling the rapid modulation of flow required to avoid target poisoning.
- Pulsed DC, RF and HiPIMS Power Options: PEM control regimes have response times fast enough to provide precise process control for a range of power supply types and deposition techniques, including High Impulse Power Magnetron Sputtering (HiPIMS).
- Advanced Sputter Source Design: KDF’s novel cathode designs are optimized for reactive sputtering by minimizing the target area subject to poisoning. While maintaining the highest sputter rates, this also reduces arcing, extending target and cathode lifetimes while improving run-to-run process consistency.
- Integrated Software Suite for Intuitive Operation: KDF’s propriety deposition system control software provide superb visual representations of process status, PEM data, and logs of all system parameters for traceability. The system is also designed to recover from faults, like running out of process gas, without compromising process integrity.
Process Development and Repeatability
One key advantage of any complex deposition system is the ability to quickly develop recipes for the deposition of new materials. KDF systems, equipped with PEM, can utilize a single emission setpoint as the central parameter for tuning a process to produce specific film compositions, reducing the need to endless process iterations to find the ‘sweet spot’.
With a ‘tuned’ process in hand, it can be run multiple cycles with minimal drift, due to the ability of the PEM system to adjust reactive gas flows to accommodate the variations in plasma composition due to target aging. This is even more critical in multi-layer, thin film stacks, like thin film batteries and solar panels, where deficiencies in one layer degrade the performance of the entire stack.
Why it Matters
The application of thin, functional, films is ubiquitous, with nearly everything in our daily lives somehow enhanced with a coating of thin films. From semiconductors, to optics, to energy generation and storage, the demand for advanced, high-precision, coatings is growing and will likely never by supplanted by other approaches. These advanced films require extreme stoichiometric controls, combined with thickness uniformity, and process reproducibility. For scientists and engineers working at the cutting edge of technology, these features are non-optional and mission critical. KDF’s fully integrated solution simplifies process development while offering unmatched speed, precision, stability, uniformity, and repeatability.
In line with Your Process
In reactive sputtering, the race is not won by speed alone – but with precision at speed. KDF’s in-line, batch thin film coating systems, with integrated Plasma Emission Monitoring, provide a robust, industry proven, platform with real-time process intelligence. The system is designed to keep reactive deposition processes in the metallic regime while achieving the highest possible deposition rates, and complete control over film stoichiometry. KDF’s advanced systems keep you in line with your process.